A Information To Deck At Any Age
페이지 정보
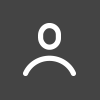
본문
Water absorption is more pronounced in WFCs with a hydrophilic matrix such as PLA and also leads to decreased mechanical stiffness and strength. WPCs do not corrode and are highly resistant to rot, decay, and marine borer attack, though they do absorb water into the wood fibers embedded within the material. One advantage over wood is the ability of the material to be molded to meet almost any desired shape. The pellets are then re-melted and formed into the final shape. In some manufacturing facilities, the constituents are combined and processed in a pelletizing extruder, which produces pellets of the new material. The most common method of production is to extrude the material into the desired shape, though injection molding is also used. Due to the addition of organic material, WPCs are usually processed at far lower temperatures than traditional plastics during extrusion and injection molding. This means that WPCs have a lower strength and stiffness than wood, and they experience time and temperature-dependent behavior. The wood particles are susceptible to fungal attack, though not as much so as solid wood, and the polymer component is vulnerable to UV degradation.
Extruded WPCs are formed into both solid and hollow profiles. WPC is more environmentally friendly and requires less maintenance than the alternatives of solid wood treated with preservatives or solid wood of rot-resistant species. New efficient and often in-line integrated production processes allow to produce stronger and stiffer WPC sandwich boards at lower costs compared to traditional plastic sheets or monolithic WPC panels. WPCs tend to process at temperatures of about 28 °C (50 °F) lower than the same, unfilled material, for instance. After a few years from the invention of the Plastic-Wood the company Icma San Giorgio patented the first process to add wood fiber/wood flour to the thermoplastics (WPCs). The company that invented and patented the process to create WPC was Covema of Milan in 1960, tote bags supplier founded by Terragni brothers (Dino and Marco). Covema called WPC under the tradename Plastic-Wood. WPC sandwich boards are used mainly in automotive, transportation and building applications, but furniture applications are also being developed. WPC sandwich boards consist of wood polymer composite skins and usually low-density polymer core which leads to a very effective increase of panel's rigidity.
WPC in a sandwich-structured composite form allows for a combination of the benefits of traditional wood polymer composites with the lightness of a sandwich panel technology. Two benefits of this, it will keep you warm if you get wet, and can make you look good. Although these materials continue the lifespan of used and discarded materials, they have their own considerable half life; the polymers and adhesives added make WPC difficult to recycle again after use. Neat polymers are polymerized without added solvents. The commonly used petroleum-based polymers have a negative environmental impact because they rely on non-renewable raw materials and the non-biodegradability of plastics. The environmental impact of WPCs is directly affected by the ratio of renewable to non-renewable materials. This includes any raw materials needed in the production of goods and services, as well as any finished goods that companies sell to consumers on the market. In addition to wood fiber and plastic, WPCs can also contain other ligno-cellulosic and/or inorganic filler materials. WPCs are produced by thoroughly mixing ground wood particles and heated thermoplastic resin. The types of plastic normally used in WPC formulations have higher fire hazard properties than wood alone, as plastic has a higher chemical heat content and can melt.
Some code officials are becoming increasingly concerned with the fire performance of WPCs. Environmental News Network, "California Fire Codes Put Focus on Plastic Decking Concerns". In February 2015, the company announced that the technology development and manufacturing parts of Plastic Logic would be separated and would go forward as independent companies, in order to generate focus while addressing a range of opportunities available in identified markets. The manufacturing plant in Dresden, Germany, which develops, manufactures and sells a range of flexible EPD, operates independently under the name Plastic Logic Germany. Kabeš and Karafiát then added bassist Tomáš Skřivánek, drummer Jan Ježek, and keyboardist Vojtěch Starý to the band's lineup and decided to continue under the name The Plastic People of the Universe/New Generation, later returning to the original name. Eva Turnová, from DG 307, became the band's new bass player. Perhaps there are a lot of factors that go into becoming a franchise player, but every legendary player definitely shares one quality, which is their skill.
- 이전글Entertainment 25.01.06
- 다음글Karaoke Bar 25.01.06
댓글목록
등록된 댓글이 없습니다.